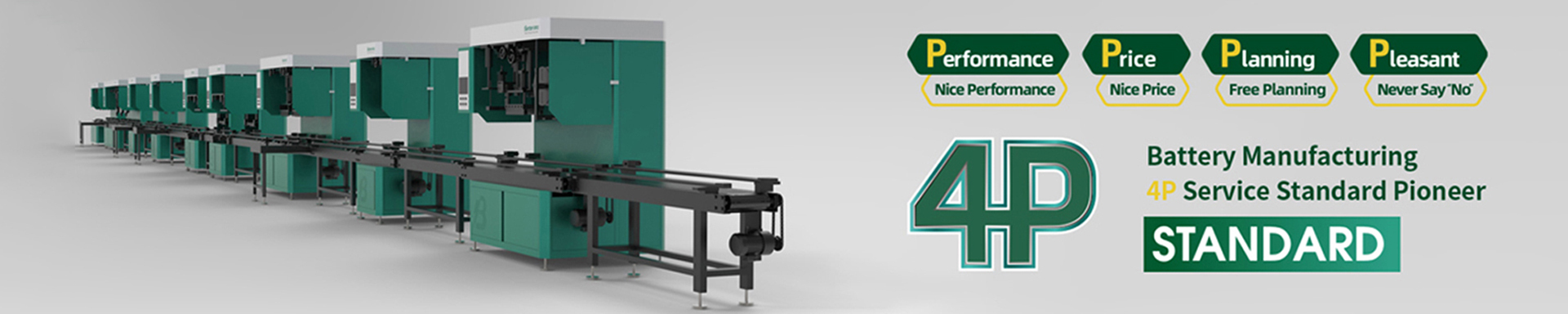
How Pressure Die Casting Machines Can Help You Reduce Your Cost and Waste in Battery Production
2023-06-22 18:00Battery production is a competitive and demanding industry that requires high quality and efficiency. However, battery production also involves high cost and waste, which can affect your profitability and sustainability. One way to reduce your cost and waste in battery production is to use pressure die casting machines. Pressure die casting machines are devices that use high pressure to inject molten metal into a mold and form a solid part. Pressure die casting machines can help you reduce your cost and waste in battery production by:
Saving your material costs
Saving your electricity costs
Saving your downtime costs
Saving your environmental costs
In this article, we will explain how pressure die casting machines can help you reduce your cost and waste in battery production in more detail.
Saving Your Material Costs
One way that pressure die casting machines can help you reduce your cost and waste in battery production is by saving your material costs. Material costs are the costs of the metal that you use to make your battery parts. Pressure die casting machines can save your material costs by:
Using less metal to make the same part
Using recycled metal to make the part
Producing less scrap metal from the part
Pressure die casting machines can use less metal to make the same part because they can inject the metal with high pressure and fill the mold completely. This means that there is no air or gas trapped in the part, which can cause defects or shrinkage. Pressure die casting machines can also use recycled metal to make the part, which can reduce the need for new metal. Recycled metal can be melted and reused in the pressure die casting machine without losing its quality or properties. Pressure die casting machines can also produce less scrap metal from the part, which can reduce the waste and disposal costs. Scrap metal is the excess metal that is left over after the part is formed and trimmed. Pressure die casting machines can produce less scrap metal because they can control the flow and speed of the metal and inject it precisely into the mold.
Saving Your Electricity Costs
Another way that pressure die casting machines can help you reduce your cost and waste in battery production is by saving your electricity costs. Electricity costs are the costs of the energy that you use to run your pressure die casting machine and melt your metal. Pressure die casting machines can save your electricity costs by:
Consuming less energy to run the machine
Consuming less energy to melt the metal
Consuming less energy to cool down the machine
Pressure die casting machines can consume less energy to run the machine because they have a high efficiency rate. Efficiency rate is the ratio of the output power to the input power of the machine. A high efficiency rate means that more of the input power is converted into output power, which means less energy is wasted or lost. Pressure die casting machines have a high efficiency rate because they have a robust and stable structure that can withstand high pressure and temperature, a precise and flexible injection system that can control the flow and speed of the metal, and a reliable and efficient cooling system that can cool down the metal and the mold. Pressure die casting machines can also consume less energy to melt the metal because they can use recycled metal, which has a lower melting point than new metal. A lower melting point means that less energy is needed to melt the metal. Pressure die casting machines can also consume less energy to cool down the machine because they have a cooling system that can regulate the temperature of the machine and prevent overheating or damage.
Saving Your Downtime Costs
A third way that pressure die casting machines can help you reduce your cost and waste in battery production is by saving your downtime costs. Downtime costs are the costs of the time that you lose when your pressure die casting machine breaks down or malfunctions. Downtime costs can affect your productivity, quality, and delivery of your parts. Pressure die casting machines can save your downtime costs by:
Having a low breakdown frequency
Having an easy repairability
Having a long service life
Pressure die casting machines can have a low breakdown frequency because they have a robust and stable structure that can withstand high pressure and temperature, a precise and flexible injection system that can control the flow and speed of the metal, and a reliable and efficient cooling system that can cool down the metal and the mold. These features can prevent or reduce common problems such as leaks, cracks, jams, or clogs in the machine. Pressure die casting machines can also have an easy repairability because they have a user-friendly and intelligent control system that can monitor and adjust the parameters of the machine, and a safety and protection system that can prevent accidents and damages. These features can help you detect, diagnose, and fix any issues or errors in the machine quickly and easily. Pressure die casting machines can also have a long service life because they have a high quality and durability. Quality and durability are the ability of the machine to perform well and last long without wearing out or breaking down. Pressure die casting machines have a high quality and durability because they are made of high-grade materials and components, and they have a warranty and service period that can cover any repairs or replacements.
Saving Your Environmental Costs
A fourth way that pressure die casting machines can help you reduce your cost and waste in battery production is by saving your environmental costs. Environmental costs are the costs of the impact that your pressure die casting machine and your battery production have on the environment. Environmental costs can affect your reputation, regulation, and responsibility as a battery producer. Pressure die casting machines can save your environmental costs by:
Producing less emissions and pollutants
Producing less noise and vibration
Producing less waste and disposal
Pressure die casting machines can produce less emissions and pollutants because they have a low energy consumption and a high recycling rate. Emissions and pollutants are the harmful substances that are released into the air, water, or soil when you use energy or materials. Pressure die casting machines can produce less emissions and pollutants because they use less energy to run the machine and melt the metal, which means less greenhouse gases or carbon dioxide are produced. Pressure die casting machines can also produce less emissions and pollutants because they use recycled metal to make the part, which means less mining or extraction of new metal are needed, which means less land degradation or water contamination are caused. Pressure die casting machines can also produce less noise and vibration because they have a robust and stable structure that can withstand high pressure and temperature, a precise and flexible injection system that can control the flow and speed of the metal, and a reliable and efficient cooling system that can cool down the metal and the mold. Noise and vibration are the loud or disturbing sounds or movements that are produced when the machine operates. Pressure die casting machines can produce less noise and vibration because they have features that can prevent or reduce friction, impact, or turbulence in the machine. Pressure die casting machines can also produce less waste and disposal because they use less metal to make the same part, use recycled metal to make the part, and produce less scrap metal from the part. Waste and disposal are the excess or unwanted materials that are left over after the part is made and need to be thrown away or recycled. Pressure die casting machines can produce less waste and disposal because they use features that can optimize the use of metal and reduce the generation of scrap metal.
Conclusion
Pressure die casting machines are devices that use high pressure to inject molten metal into a mold and form a solid part. Pressure die casting machines are useful for battery production, as they can produce complex and precise parts with high quality and efficiency. However, pressure die casting machines can also help you reduce your cost and waste in battery production by:
Saving your material costs
Saving your electricity costs
Saving your downtime costs
Saving your environmental costs
By using pressure die casting machines, you can not only improve your quality and efficiency, but also save your money and resources, as well as protect your environment. Pressure die casting machines are a smart choice for battery production.