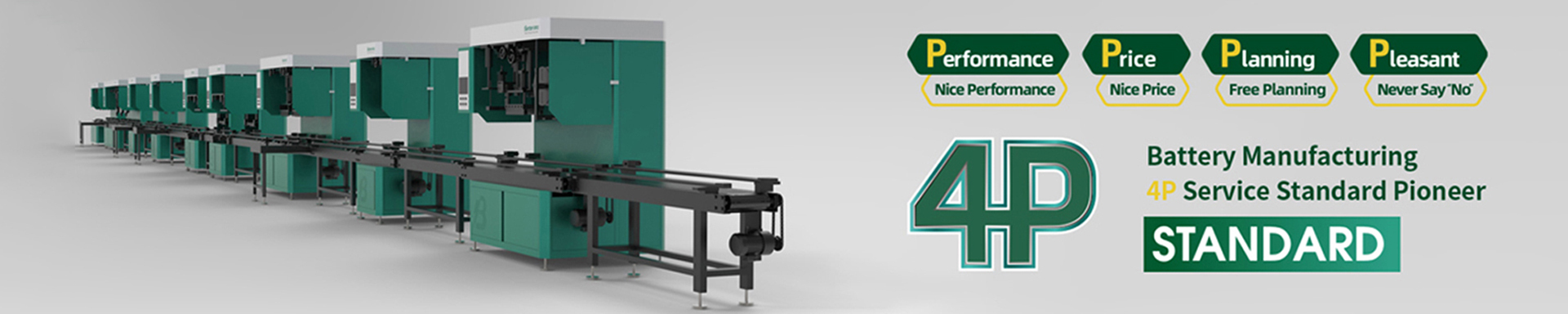
Battery Plate Production: Stepping Up with a Continuous Pasting Line
2025-04-29 16:00In the competitive landscape of battery manufacturing, efficiency, consistency, and cost control are paramount. One of the most critical stages is applying the active paste material to the battery grids. Traditional methods can be labor-intensive and sometimes lead to variations. This is where modern automation steps in, specifically with the Continuous Pasting Line.
So, what exactly is this system? Imagine a seamless, automated process that takes raw expanded battery grids and transforms them into fully pasted, dried, and neatly stacked plates, ready for the next stage. That's the essence of a Continuous Pasting Line. It’s designed specifically for the grids produced by expanding lines, creating a highly efficient workflow.
Why Make the Switch? The Advantages Are Clear
Moving to a continuous system isn't just about speed; it's about fundamentally improving your entire plate production process. Here’s how our advanced line delivers tangible benefits:
End-to-End Automation: This isn't just one machine; it's a fully integrated production line. It handles everything from unwinding the expanded grid material right through pasting, precision cutting (incorporating the function of a dedicated cutting machine), rapid drying in a specialized section akin to a flash drying oven, and finally, high-speed stacking. This comprehensive automation dramatically increases throughput and reduces manual handling points.
Significant Labor Savings & Cost Reduction: Remember the days of needing multiple operators for separate pasting, drying, and handling steps? This line changes the game. The entire process can be managed by just 3 to 4 operators (including those managing the stacked plates). This directly translates to lower production costs per battery.
Enhanced Plate Uniformity: Continuous processing inherently leads to greater consistency. By maintaining constant speed and pressure during pasting and controlled conditions through drying, you achieve a higher degree of uniformity from plate to plate compared to batch processes. This is crucial for final battery performance and lifespan.
Clean, Efficient 'Cold Processing': A major advantage is that the entire operation is a cold process. This means no pollution associated with heating lead and, crucially, no lead loss during pasting. It's a cleaner, safer, and more environmentally conscious approach to manufacturing.
Smart Stacking & Handling: The integrated plate stacking device isn't just a simple collector. It includes a cleaning unit and can pre-arrange the plates during stacking. This thoughtful design reduces the downstream labor intensity and ensures plates are handled correctly from the moment they exit the line, preparing them efficiently perhaps for processes sometimes handled by equipment like a Rotary plate divider in different setups, but integrated here for smoothness.
Reliable PLC Control: The entire line operates under sophisticated PLC control, ensuring all components work in harmony. This provides advanced, reliable operation and makes process monitoring and adjustments straightforward.
Quick Questions You Might Have:
What does it do start-to-finish? It unwinds grid material, applies paste, cuts it into plates (like a cutting machine), dries them quickly (similar to a flash drying oven), and stacks them neatly.
Adopting a Continuous Pasting Line represents a significant leap forward for battery manufacturers using expanded grids. It streamlines production, drastically cuts down on labor requirements, enhances plate consistency, and promotes a cleaner, safer working environment. By integrating pasting, cutting, drying (like a flash drying oven), and stacking (managing the separation function that might otherwise use a Rotary plate divider), this automated system offers a powerful solution for boosting efficiency and quality.
If you're looking to modernize your plate production, reduce costs, and improve uniformity, investing in a Continuous Pasting Line is a strategic move that pays dividends in today's demanding market.